THANK YOU FOR SUBSCRIBING

The IoT is Reality in Industrial Applications
Bob Karschnia, VP Wireless, Emerson Process Management

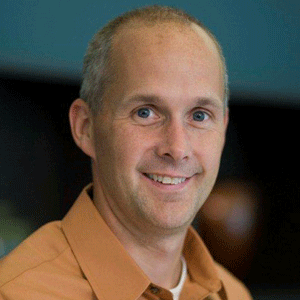
Bob Karschnia, VP Wireless, Emerson Process Management
The Internet of Things (IoT), sometimes referred to in the industrial sector as the Industrial IOT(IIOT), is much further advanced than in the commercial realm. The main reason is the prevalence of the IoT foundation in the industry, namely connected sensors, which are the “things” in the IoT. Without these connected sensors, there can be no IoT, which is why many commercial IoT discussions focus on future applications, instead of the here-and-now found in the industrial world.
Outside of cars and trucks, connected sensors in the commercial world are not common. Most sensors are either not connected, like a thermometer mounted on a wall, or are simply part of a single and simple unconnected device, like a thermostat. And despite the entire buzz about smart thermostats, very few are connected.
By contrast, there are hundreds of millions of connected wired and wireless pressure, level, flow, temperature, vibration, acoustic, position, analytical and other sensors installed and operating in the industrial sector, with millions more added each year.
These sensors connect through wired and wireless networks, often Ethernet-based, to a variety of higher level software platforms. This secure data connectivity can be to either local or remote software platforms. For remote software platforms, data storage, and computing can be done in the cloud.
These higher level software platforms include control and monitoring systems, asset management systems, and specialized data analysis systems. When data analysis systems are remote, sophisticated big data analytics are performed by dedicated experts to reveal patterns, problems and solutions.
To summarize, the IoT in the industrial world is used to connect sensors to big data analytic and other systems to automatically improve performance, safety, reliability and energy efficiency by:
► Collecting data from sensors (things) much more cost
effectively than ever before because sensors are often battery-
powered and wireless
► Interpreting this data strategically using big data analytics
and other techniques to turn the data into actionable
information
► Presenting this actionable information to the right person,
either plant personnel or remote experts, and at the right time,
and
► Delivering performance improvements when personnel take
corrective action.
As with many things, the industrial it comes to life with specific application examples, here are a few.
Ergon Refining’s Vicksburg, Miss. facility implemented an industrial IoT
“In the industrial sector, hundreds of millions of connected sensors are currently installed with millions more coming online annually”
The asset management system analyzes the big data from the sensors and transforms it into actionable information which is delivered to plant personnel in one of two ways. Control room operators view this information on their PC-based human machine interface monitors, as do other plant personnel on office PCs connected to the Ethernet plant network. Mobile workers view this information on handheld industrial PCs connected to a plant wide Wi-Fi network powered by Cisco industrially-hardened access points.
The following reduced CapEx costs were realized:
► Significantly reduced sensor installation costs using
wireless networks
► Calibration checks that are four times faster, but require only
one-third as many staffers, and
► Wired and wireless networks reduced wiring costs and
improved diagnostic capabilities as compared to traditional
hardwired solutions
And these OpEx benefits were realized:
► Increased production capacity while avoiding capital
investments through wireless tank level monitoring
► Improved safety through vibration monitoring in
difficult to access locations, and
► Energy savings enable by wireless steam trap
Monitoring.
Now that the infrastructure is in place at Ergon’s facility for data collection, analysis and distribution—it’s a simple matter to add other wireless sensors to leverage the initial investment and create more value.
Many other industrial facilities are implementing their own industrial IoT, and one such application is steam trap monitoring via wireless acoustic transmitters. Acoustic sensors and specialized big data, software analysis systems, often located remote from the plant and connected to the sensors via the Internet, detect steam trap problems automatically and alert plant personnel so they can take action.
By monitoring a plant’s steam trap and its steam distribution system automatically and continuously via an IoT application, energy losses costing up to $30,000 annually per steam trap can be eliminated. As many plants have scores of steam traps, savings can be considerable.
For example, a plant was experiencing a 15 percent annual steam trap failure rate, with 12.5 percent of the plant’s steam traps responsible for 38 percent of the steam loss. Correcting this issue with wireless steam trap acoustic sensors and accompanying big data analytics resulted in an annual savings of $301,108 and a payback period of just a few months.
Another industrial IoT example is monitoring valves controlling gas flows to flare stacks in refineries. Using wireless acoustic transmitters, one refinery was able to improve regulatory compliance and reduce hydrocarbon losses by $3 million annually due to timely detection and repair of faulty valves. The project paid for itself in five months, with an estimated annualized ROI of 271 percent annualized over 20 years.
In the commercial realm, the IoT is in the conceptual stage, with many possible permutations discussed—but with few installations up, running and delivering value. But in the industrial sector, hundreds of millions of connected sensors are currently installed with millions more coming online annually.
Many of these sensors are wireless because they cost much less to install than their wired equivalents. These low cost wireless sensors are securely connected via mesh networks to systems performing big data analytics to dramatically improve plant performance, resulting in payback periods measured in months, with ongoing savings afterwards.
See This: Energy Tech ReviewWeekly Brief
I agree We use cookies on this website to enhance your user experience. By clicking any link on this page you are giving your consent for us to set cookies. More info
Read Also
